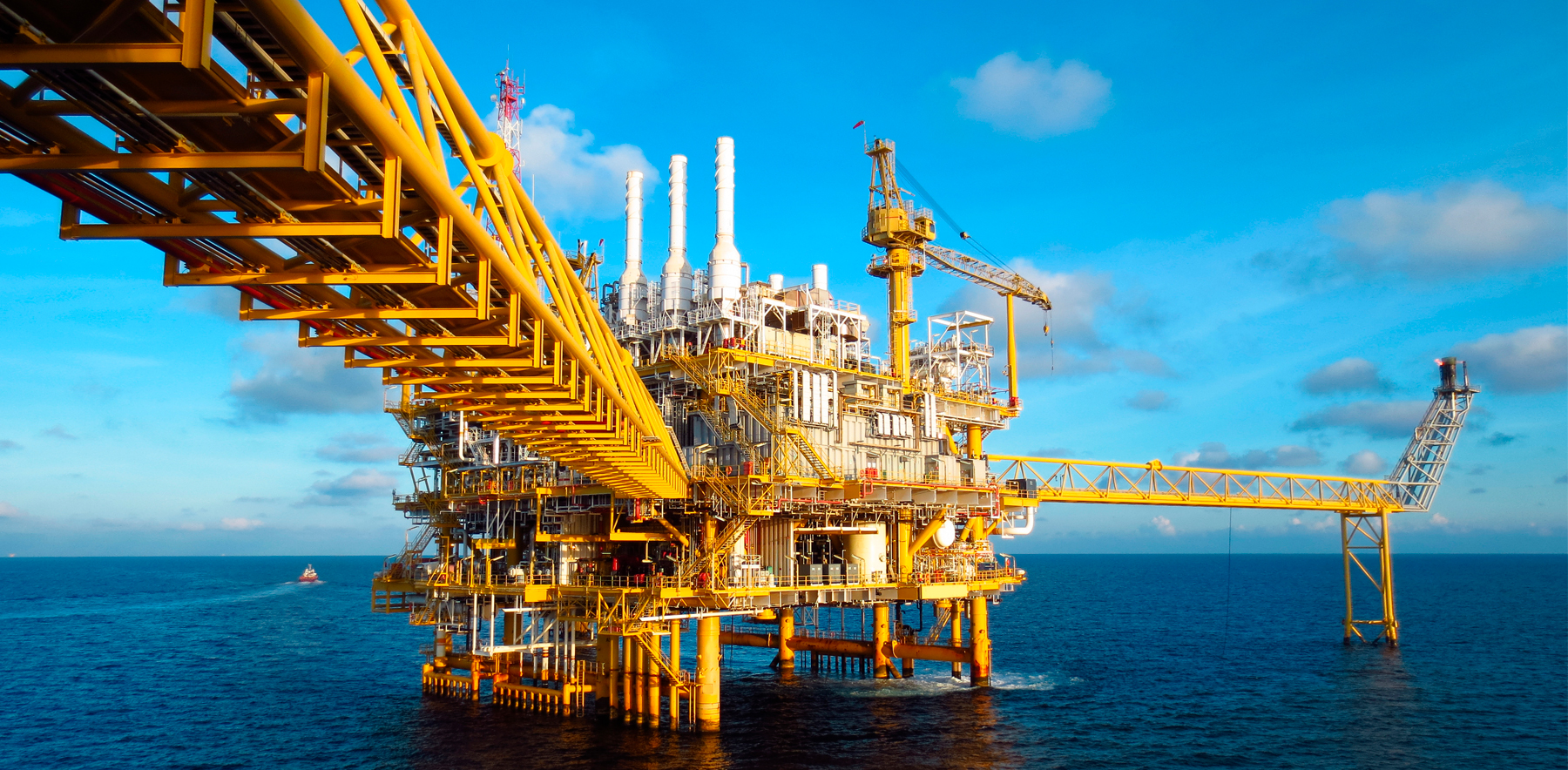
What you need to know about the SEMS certification audit
The Safety and Environmental Management System is a performance-focused tool for integrating and managing offshore operations. Its purpose is to enhance operations’ safety by reducing incidents’ frequency and severity.
Objectives
- Focus attention on the influences that human error and poor organization have on accidents.
- Continuous improvement in the offshore industry’s safety and environmental records.
- Encourage the use of performance-based operating practices.
- Collaborate with the industry in efforts that promote the public interests of offshore worker safety and environmental protection.
History
The Safety and Environmental Management Program (SEMP) was developed in 1993 as a voluntary adherence to the offshore oil and gas industry. The Minerals Management Service (MMS) was the first entity responsible for regulation, but eventually, the Bureau of Ocean Energy Management Regulation and Enforcement (BOEMRE) took its place. Later, the agency split into three different ones: Office of Natural Resources Revenue (ONRR), Bureau of Ocean Energy Management (BOEM), and Bureau of Safety and Environmental Enforcement (BSEE).
In April 2010, the Deepwater Horizon disaster caused a massive oil spill devastating ocean life and the economy of many coastal communities in Florida, Texas, and Louisiana.
This event prompted the COS to adopt and revise the SEMS program as we know it now, which applies to oil, gas, and sulfur operators on the outer continental shelf.
The SEMS Program
The Center for Offshore Safety (COS) incorporates the American Petroleum Institute’s Recommended Practice 75 (API RP 75) and 30 CFR Part 250, Subpart S, for developing a Safety and Environmental Management System for Offshore Operations and Facilities, including a complete SEMS program. Its principal intent is to hold operators accountable for the safety of the offshore facility, assuring that all contractors and subcontractors have safety policies and procedures in place.
The operators must implement a program that “identifies, addresses and manages safety, environmental hazards, and impacts during design, construction, startup, operation, inspection and maintenance of all new and existing facilities.” There are also elements intended to prevent significant scale events like fires, explosions, and spills that could affect the platform’s safety or the environment.
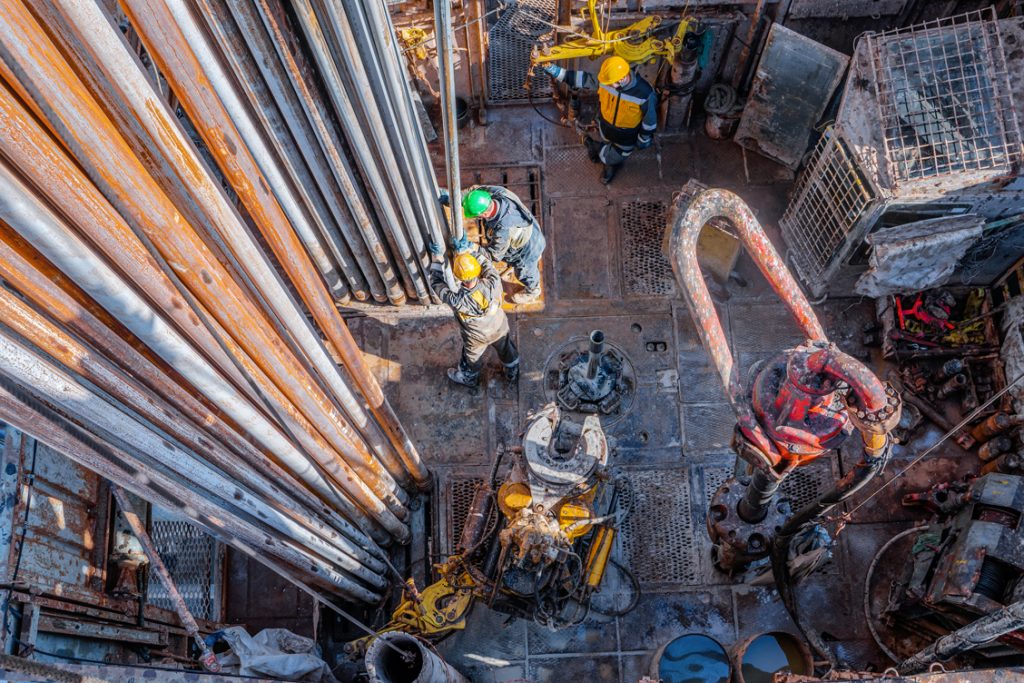
Elements
- General: Designation of responsibilities, overall training and expertise, and requirement of all written SEMS policies, practices, and procedures.
- Safety and environmental information: Requirements for a written report describing the facility’s design, construction, and operation.
- Hazards analysis: Implementation of a hazard analysis (facility-level) and a job-safety one (operations level) to ensure that all recommendations are resolved and documented.
- Management of change: Development and implementation of written management of change procedures associated with equipment, operating procedures, personnel changes, contractors, materials, and operating conditions. These must include a technical basis for the change and its impact on safety, health, and the environment.
- Operating procedures: Developing and implementing written operating procedures that provide instructions for conducting safe and environmentally sound activities related to initial startup, routine and emergency operations, startup following a turnaround, an emergency shutdown, and bypassing and flagging out-of-service equipment. Operators also require to discuss the safety and environmental consequences of deviating from regular procedures and the hazards presented by the chemicals used in the operations.
- Safe work practices: General requirements for safe work practices, minimization of risks associated with operations, and handling of materials and substances that could affect the environment.
- Training: Requirements for a training program, so all personnel receives training according to their duties and aware of potential environmental risks. This training must address operating procedures, safe work practices, emergency responses, reporting of unsafe work conditions, and hazard identification.
- Assurance of quality and mechanical integrity of critical equipment: Applies to all facility equipment and systems that prevent or mitigate uncontrolled releases of hydrocarbon, toxic materials, or others that can have safety or environmental impacts. This part includes provisions for written procedures, training or maintenance personnel, deficiency management, and quality assurance for the design, fabrication, installation, and spare parts for OCS facility equipment.
- Pre-startup review: Environmental review for new and modified facilities. The process must ensure that the construction and equipment comply with specifications and that safety, environmental, operating, maintenance, and emergency procedures are in place.

See also: What you need to know about the SASISOPA certification audit
- Emergency response and control: Implementation of emergency response and control plans. These must include requirements for drilling and evacuation procedures.
- Investigation of incidents: Procedures for investigating incidents that had safety and environmental consequences. The study must determine the nature of the event, the factors that caused its initiation and escalation, and recommend system changes. Near misses are also a reason for starting an investigation.
- Audit: All operators must undergo an independent audit within two years of the initial implementation of the SEMS program and every three years afterward. The operator submits the plan to the BSEE 30 days before the audit; the bureau reserves the right to modify the list of facilities that the operator proposes. The evaluation is performed on 15% of the operator’s platforms. The operators must submit an audit report and a plan for addressing the deficiencies for review within 60 days after the audit.
- Recordkeeping: Operators must ensure that all documents are kept for six years; individual records must be maintained only for two years. These must be ready upon request by the BSEE.
- Stop-work authority: Operators must ensure that they can stop or decline to perform a process that represents an imminent risk to all personnel.
- Ultimate work authority: Operators must have a process that identifies the individual with the final authority at the facility and over the operation. Personnel needs to know who is in charge of a specific operation at all times. This person also needs to have the authority given by the operators to take whatever action is required to mitigate and abate the conditions causing an emergency.
- Employee participation plan: Management must consult with its employees on the development, implementation, and modification of the SEMS program and develop a written plan for how they will participate. Employees must also have access to sections of the SEMS program that are relevant to their Jobs.
- Reporting unsafe work conditions: Operators must implement procedures for all personnel to report dangerous work conditions. The information then must be placed in a visible location.
What happens before, during, and after a SEMS certification audit?
The BSEE is the entity in charge of evaluating the operator’s compliance with the SEMS standard; in other words, protecting worker safety and the environment.
If the inspector finds any violation during a SEMS certification audit, the BSEE can issue an “incident-of-noncompliance”, impose monetary penalties, or rescind the operator’s lease.
Depending on the violation, the BSEE can issue a “warning or shut-in INC” during a SEMS certification audit:
- Warning INC: Violation is not severe. The operator will have to correct it as soon as possible (14 days usually).
- Shut-In INC: Violation is severe and poses a danger to employees and the environment. The suspension of operations will be in the nation’s interest. The breach must be corrected to continue operations.
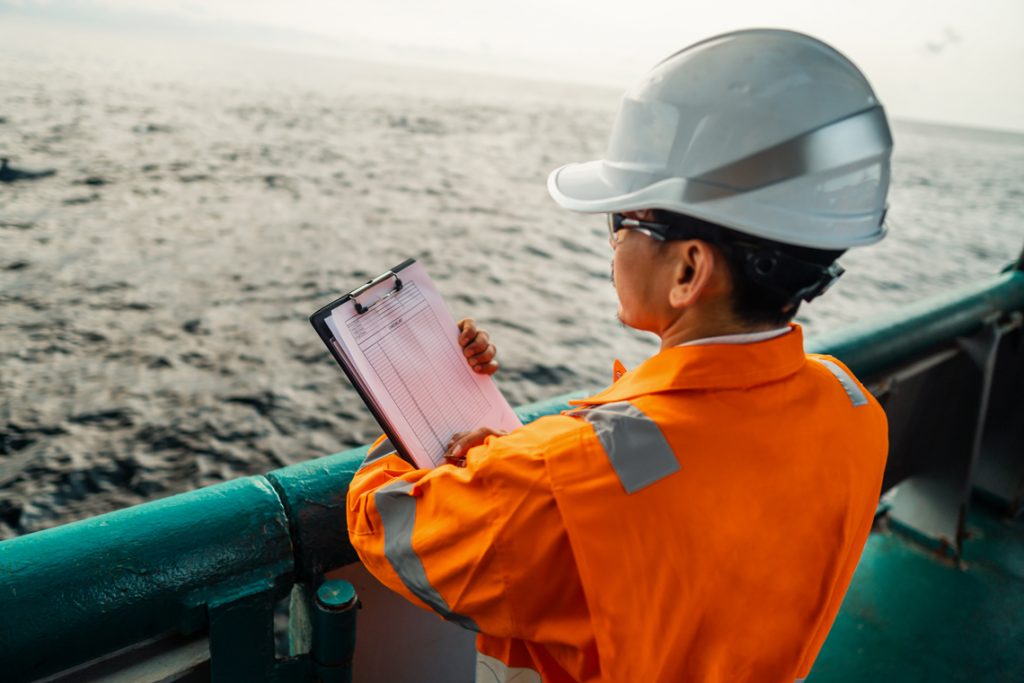
Penalties can go up to 40,000 USD per day if the violation is not corrected within the specified time, or if it’s a serious threat to employees and the environment.
The operator has 30 days to request a meeting with a reviewing officer, submit information, or pay the fine. Then, the officer will decide if there’s a need for a final penalty. Meanwhile, the BSEE can start disqualification procedures against the offshore operator. If the threat is still there or a dangerous activity has not stopped, the lease or permit could be canceled.
Finally, the BSEE may involve the Department of Justice if there are signs of negligence.
The operator has the right to initiate an appeal process and request a hearing.
Finding the right company to ensure that you meet your SEMS certification audit goals and BSEE’s expectations can be tricky. Still, CICS Americas approach lets you identify risk areas and improve your system for the protection of your employees and the environment.
Source: BSEE