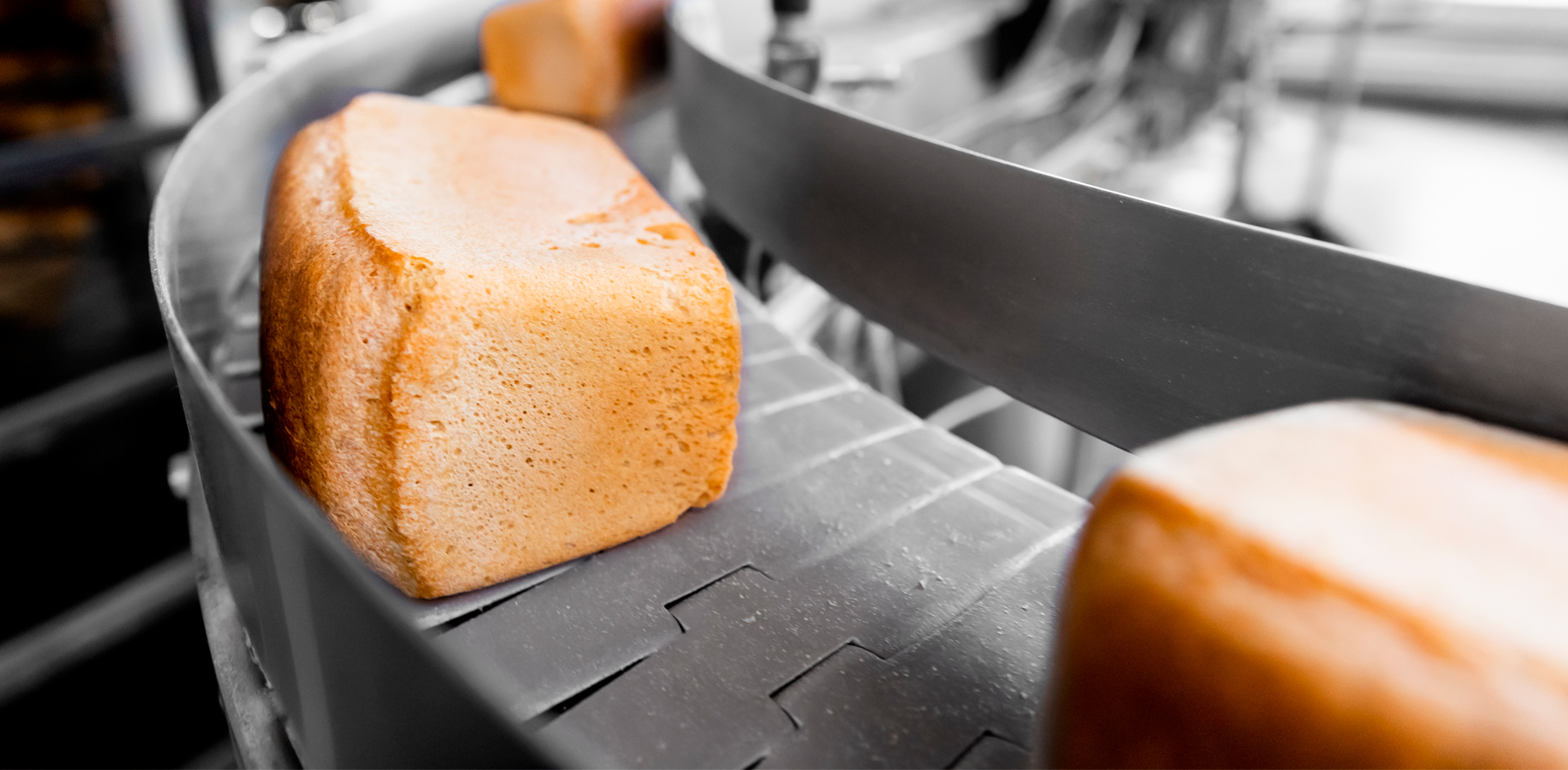
What you need to know about the SQF certification audit
As a customer, you expect food products provided by retailers to meet all quality and safety specifications. They, in turn, expect the same from providers. Maybe in the past, you’ve heard news of recalls from supermarkets or manufacturers withdrawing a specific food product considered unsafe after an investigation. The SQF Program prevents all of this. Throughout this article, you’ll learn more about it and the certification around it, which proves your business complies with all the safety regulations.
What is the SQF Program?
The Safe Quality Food (SQF) Program is a food safety and quality plan recognized by retailers and foodservice providers worldwide. SQF codes are designed to meet industry, customer, and regulatory requirements for all the food supply chain sectors.
The SQF standard, first developed in Australia in 1994, has been owned and managed by the Food Marketing Institute (FMI) since 2003. The program arrived in the U.S. in 2005. Under pressure from the FMI, retailers all over the country began adopting it in 2007.
Rigorous farm-to-fork safety and quality certification allow producers to ensure their customers that their food products meet the highest possible standards.
The SQF Program guides companies by setting up a comprehensive food safety management system on their farms, warehouses, or facilities by assessing their processes through an annual audit. Passing it results in the SQF certification.
Considerations
The SQF Program has three variants that businesses can choose from depending on their needs:
- SQF Food Safety Fundamentals Program: For small and developing businesses that don’t have a robust food safety management program in place or want to take their existing program to the next level.
- SQF Food Safety Program: For sites looking to get a GFSI-benchmarked certification. The SQF Food Safety Program provides sites with a HACCP (Hazard Analysis and Critical Control Points) based approach to ensure their products meet regulations.
- SQF Food Safety and Quality Program: For companies that have been SQF certified and would like to improve beyond what they have already mastered.
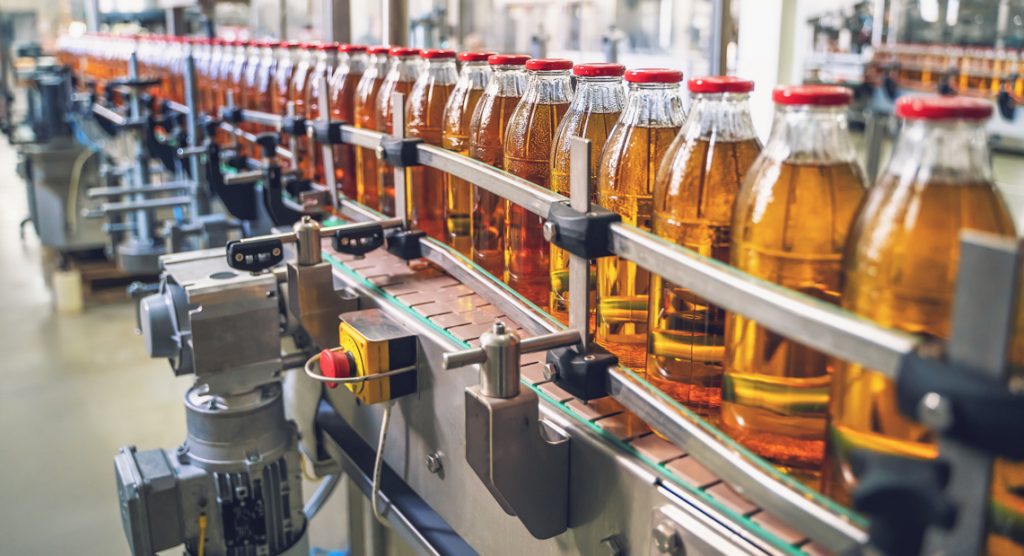
What’s next? The steps towards the SQF certification audit
- Choose an employee as the SQF leader: This person needs to receive HACCP training and be competent enough to implement the SQF system requirements and food safety plan.
- Document and implement according to the SQF code: To achieve the SQF certification, you must document and implement the system elements and relevant GMP (Good Manufacturing Practices) modules of the SQF code.
- Document: Policies, procedures, work instructions, and specifications that meet the system elements and GMP modules of the SQF code.
- Implement: Execute all of the above and keep records to demonstrate compliance with the relevant modules of the SQF code.
- Choose a certification body: Contact CICS Americas, complete the questionnaire, and return it for a formal proposal. Then, an experienced SQF registered auditor performs the evaluation.
- Conduct a pre-audit (optional): This step will allow you to identify all the gaps between your program and the SQF code; in other words, procedures, documentation, and practices that do not satisfy the standard.
- Schedule your audit.
The SQF certification audit begins
The SQF certification assessment consists of two steps:
- Documental audit: Carried out to assess and confirm that the Management System documentation meets all the SQF code requirements. This step can be conducted offsite.
- Site audit: carried out to evaluate and verify the effective implementation and maintenance of the Management System.
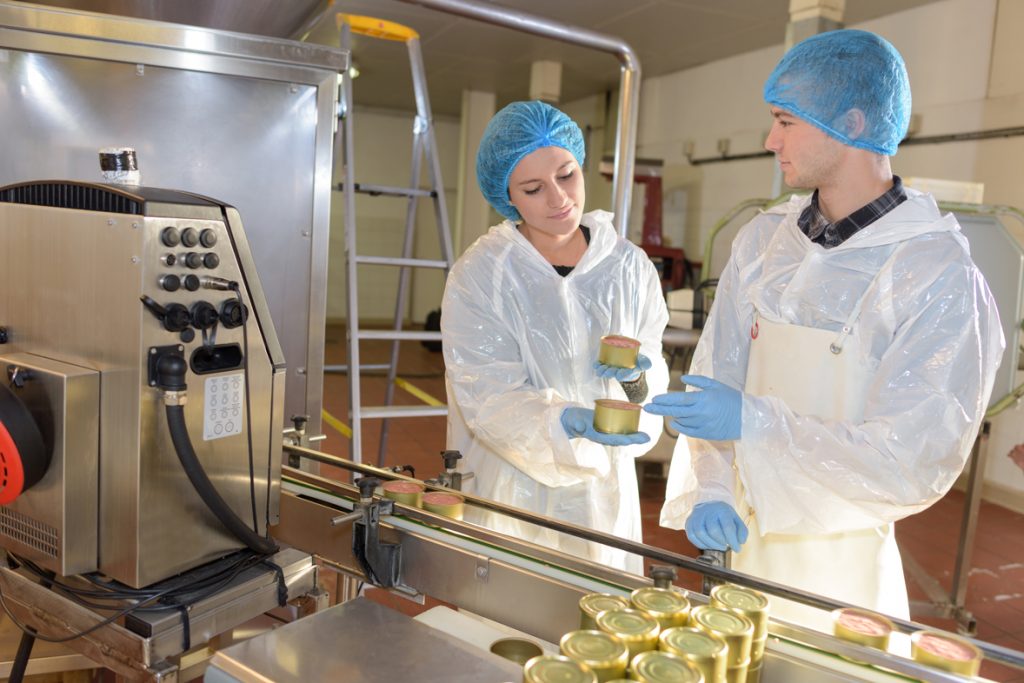
See also: SQFI Certificate Extension Policy and risk assessments: what you need to know
What happens before, during, and after evaluation day?
- Before: Your assigned auditor sends the audit plan one week before the scheduled visit for your desk audit.
- During: The auditor tours the site, reviews documents, gathers evidence, has team meetings, and provides the non-conformities (if applicable). The following elements will be evaluated (other items can be considered depending on the type of business):
- Management commitment.
- Document control and records.
- Specification and product development procedures.
- Food safety system.
- SQF system verification.
- Product identification, trace, withdrawal, and recall procedures.
- Food defense and fraud procedures.
- Allergen management.
- Training.
- After. The report is submitted for technical review and also delivered to you. Then, the Corrective Audit Report is handed. This document contains all the corrective actions required for compliance with the SQF code. Before the 30-day deadline, the auditor approves the corrective actions. Finally, Certificate Decision reviews the documentation. If you achieve a “C-Complies” or higher, you will obtain the SQF certification.
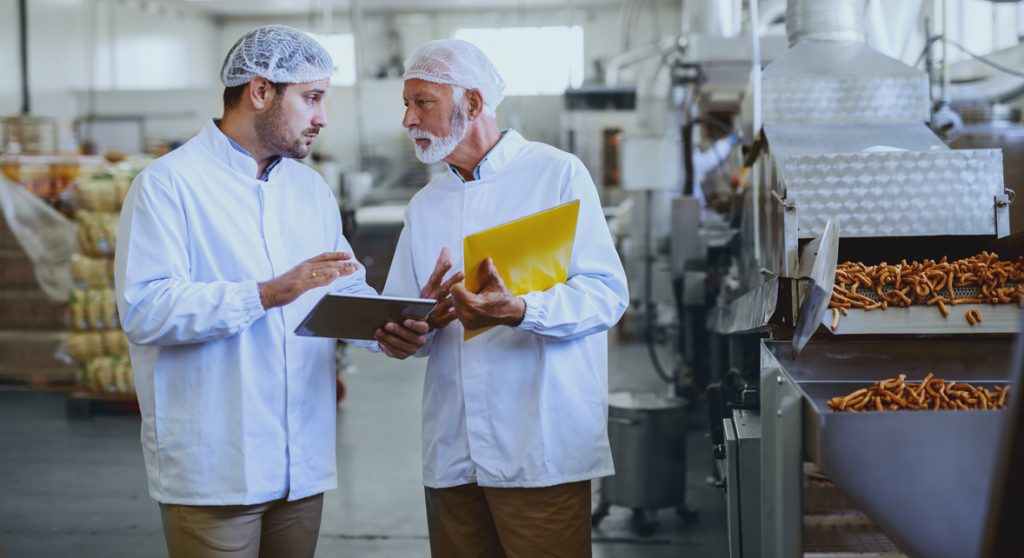
What are non-conformities?
In the SQF certification audit, a non-conformity is any irregularity found in the system that needs to be addressed to comply with the SQF code. The auditor shall advise the business of the quantity, description, and extent of the non-conformities, which can be graded as minor, major, and critical.
The more critical the non-conformity, the sooner it needs to be addressed.
How long will the evaluation take?
The duration depends on the size and complexity of the plant site.
Basic duration:
- Step 1: one day.
- Step 2: two days.
Scores and rating
A scale of 0 to 100 determines the evaluation score—every non-conformity results in point loss.
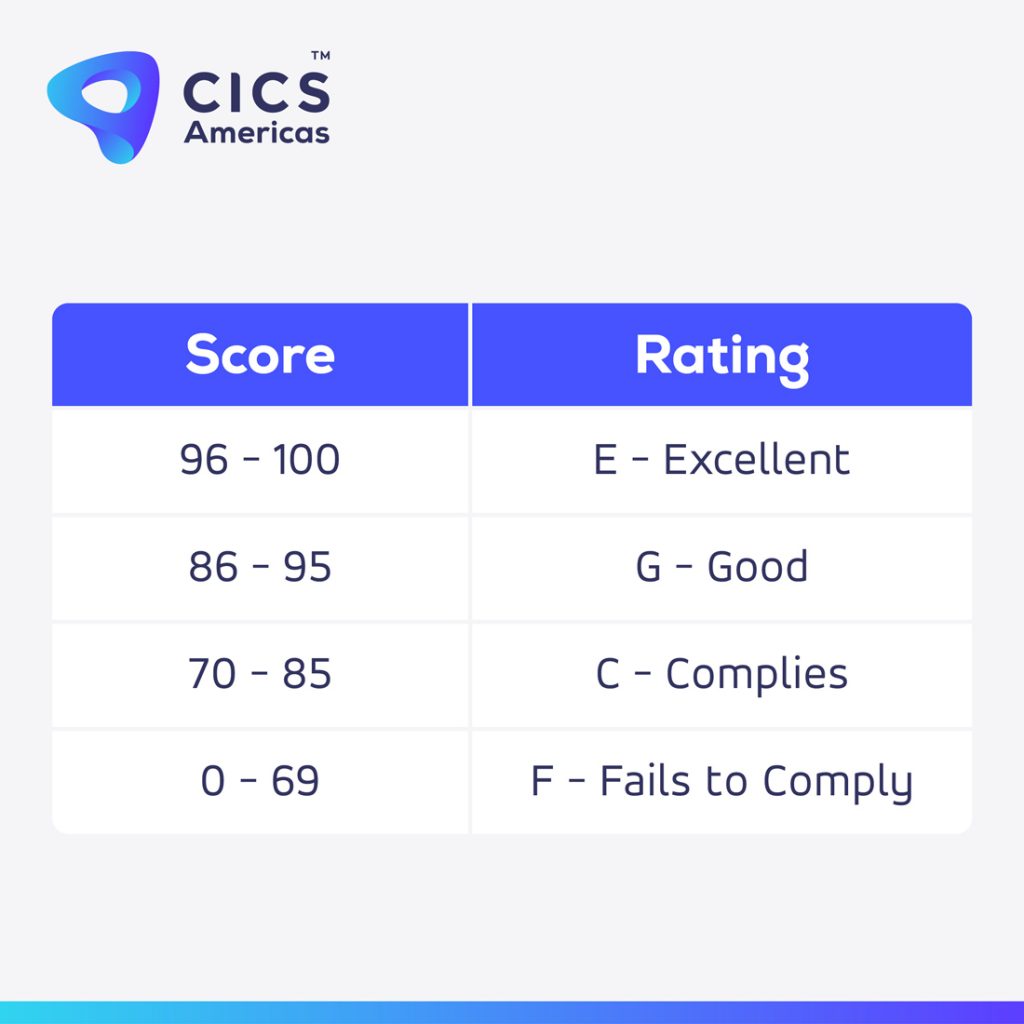
Audit Score
A “Fails to Comply” rating indicates that you cannot receive the certification and need to reapply for a new evaluation. SQF certification is valid for one year.
Obtaining an SQF certification means you care about your customers and your food products’ quality and safety.
Source: SQF Institute